VDC Services Save Multifamily Development Project $1.8M in construction delays
Our New Initiatives Division develops a Civil Infrastructure Modeling (CIM) project execution plan with VDC services to create 3D modeling - saving our client in construction delays, reducing rework and change orders, streamlining material selection with better cost control, and optimizing supply chain visibility.
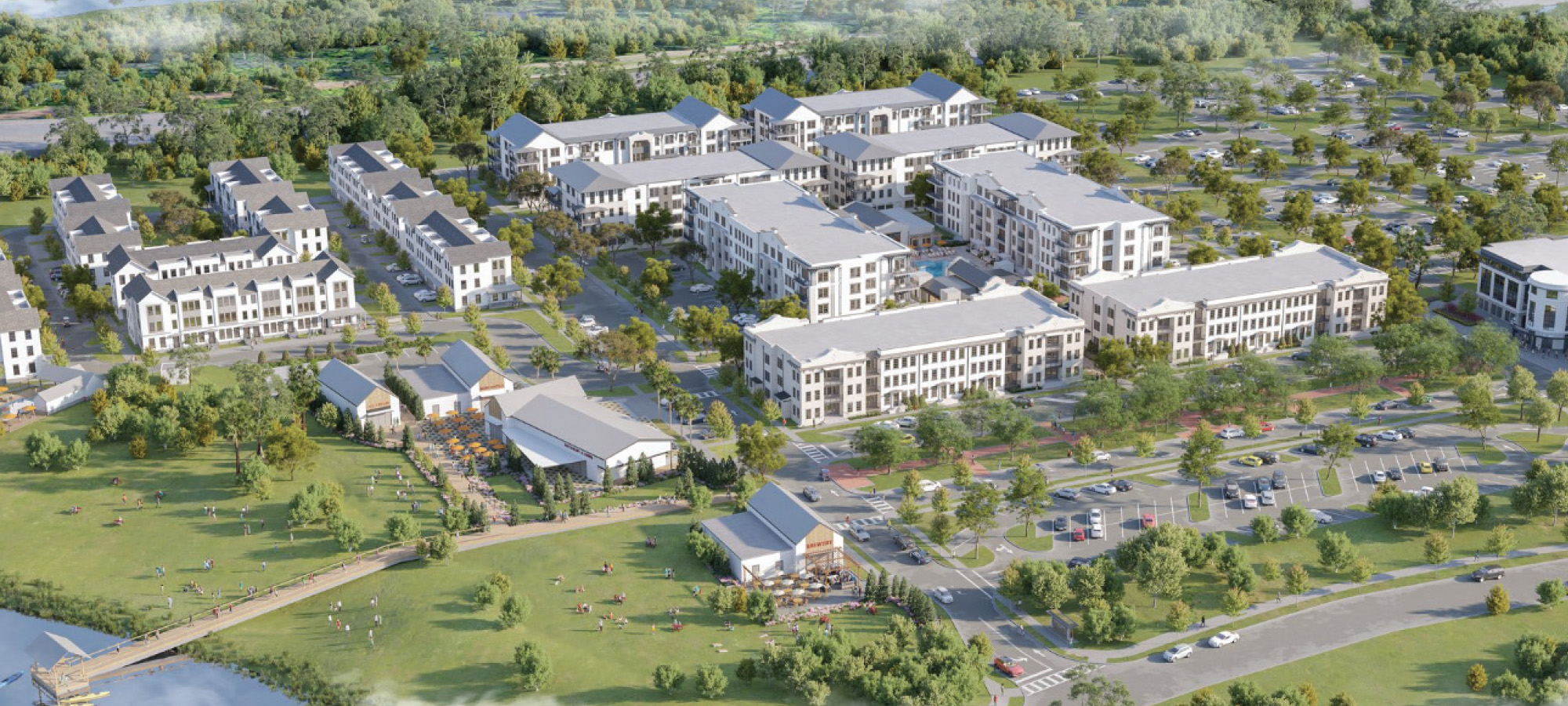
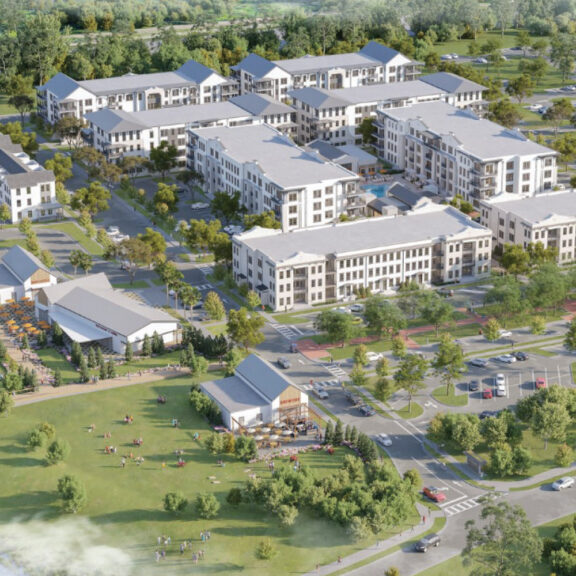
Project Overview
This project was large in scale, including four parcels totaling 8.98 acres and eight 3- or 4-story multi-family residential buildings with a total of 320 apartments. It also included two one-story amenity buildings, a clubhouse, a leasing office, and more. Not only was a phased demo of existing water, storm, sewer, and fiber optic required, but new water, storm, sewer, and electrical were required. All of this needed expertly coordinated with services for an ongoing project on an adjacent parcel.
Challenge
The site sat on the old Charleston Battery Soccer Field (MUSC Health Stadium), which created unknown variables. Existing water, storm, sewer, and fiber optic lines needed removal or to be phased out and new, more sophisticated systems needed to be phased in. Existing services coupled also with an adjacent (Parcel K South) infrastructure project that Gantt’s right on top of their project’s new site construction. It became apparent to WM Jordan’s team that this project’s variable needed to be controlled. Factors such as the existing conditions, truncated time schedule, and pending construction on adjacent parcels necessitated an innovative approach to ensure the critical path to construction was met.
Project Scope
Because this site sat on the old Charleston Battery Soccer Field (MUSC Health Stadium), there were a variety of unknowns. Existing utilities needed removed and new, more sophisticated systems needed phased in. Because all the existing services also coupled with an adjacent parcel, it became apparent to WM Jordan’s team that project variables needed controlled. Challenging existing conditions, a truncated time schedule, and pending construction on the adjacent parcel meant an innovative approach was crucial to completing this project on time.
Method
WM Jordan decided to work with our New Initiatives Division to develop a Civil Infrastructure Modeling (CIM) project execution plan and with VDC services to create a 3D model. The initial pass of drawings included a “constructability takeoff” or “quantity takeoff,” where we reviewed local specs and drawings, running through all the C drawings and services to build a list of materials for the project, to specification, right down to bolts and gasket packs. From there, Ferguson Waterworks moved into 3D Modeling, where we weened out any low-hanging RFIs that needed to be addressed. As the teams were making their own internal observations, asking questions, and sharing data, it became apparent that sharing information across teams was critical to success. A weekly cadence of findings meetings was implemented and these weekly meetings later became a more classic BIM/MEP type of coordination, clash resolution meeting.
Solution
According to WM Jordan, “By knowing the UG conditions in relation to foundations and future utilities allowed us to add clarifications in the contract to protect us from delays and costs.” They went on to say that “the Ferguson team was able to find design issues that could have added about $1.8M in construction delays to the Nowell Creek Project.” As a result of this partnership and professional VDC services, there was less rework, fewer requests for information, fewer change orders, better cost control, streamlined material selection, earlier material cost analysis, and better supply chain visibility.
Product Advantages
– Working with Ferguson Waterworks to model all the utilities accurately to code, practice, field, and cost
– The initial pass of drawings included a “constructability takeoff” or “quantity takeoff,” where Ferguson Waterworks reviewed local specs and drawings and ran through all the C drawings to build a list of materials for the project, per specification.
– Identifying and addressing all low-hanging RFIs before 3D scanning services
– A weekly cadenced findings meeting was implemented to promote asking questions and sharing data across teams
View Similiar Case Studies
In order to revitalize and meet stormwater codes, the abandoned parking area at the Shoppes at Fashion Square in Orlando, FL, required updates. With a permeable paving system and machine technology, we helped the client achieve their goals, save $1 million, and complete the project in just 10 days.
With solar panels in place and operational, an immediate and effective erosion control solution was imperative. Especially considering the panels were positioned next to channels, drip lines, and spillways.
After failed attempts to stabilize the earth at the Mt. Jackson Solar Farm, they required an immediate, cost-effective erosion control solution. Ferguson Waterworks was brought on board to address their ongoing concerns.